This article delves into machining tools and techniques. You can check out the previous parts here:
⇒ Searching for the Isolated Island of the Great Ocean - Atlansia - Part 1
⇒ Searching for the Isolated Island of the Great Ocean - Atlansia - Part 2
⇒ Searching for the Isolated Island of the Great Ocean - Atlansia - Part 3
- Part 4 Contents -
Cheena: Last time, we ended up going off on a tangent. Where should we start this time?
Nemoto: Hmm... Not many people might be interested in this, but how about discussing manufacturing methods and machining tools?
1 - Atlansia Crafts & Machines
Cheena: Machining tools! It’s definitely going to be an interesting discussion, but figuring out where to start is tricky.
Should we begin with construction methods and instrument-related technology?
Nemoto: Yeah, sounds good. We’ll probably jump around a lot, so let’s cover the essential points first.
Cheena: How about we start with how the truss rod is embedded and the use of support rods?
Generally, a truss rod is installed by cutting a groove in the front of the neck’s main wood and covering it with the fingerboard, or by inserting it from the back and sealing it with a skunk stripe. However, at Atlansia, the rod is inserted straight through a hole drilled from the neck end. (No.3, PAT.1421968) This is said to have acoustic advantages, but I can’t help but wonder—wouldn’t replacing the rod be a huge hassle?
Nemoto: Yeah, when I first heard about it, I was like, “Wait, what?” Replacing the rod does sound like a pain, but maybe they have a workaround. Atlansia seems pretty confident in the neck’s strength, so they might think there’s no need to ever fully adjust the rod.
Cheena: I might include a separate article later with patent documents. There could be some internal mechanism that prevents vibrations even without fixing it in place.
By the way, the support rods—there are two of them—are inserted from the back of the neck. The strength must be incredible; there’s a pretty famous photo of Atlansia’s founder, Mr. Hayashi, hanging from a horizontally placed neck!
*Atlansia’s Official Facebook:
https://www.facebook.com/334082209985909/photos/pb.100079886373939.-2207520000./522894467771348/?type=3
https://m.facebook.com/334082209985909/photos/a.342059922521471/1077211085673014/?type=3
I’ve also seen customer reviews saying the neck is so strong that they’re unsure if the rod even works.
Nemoto: That photo honestly looks like a joke at first glance.
For six-string necks with support rods, there are (obviously) two wooden inserts. Since I didn’t know about the support rods at first, I was really surprised—like, what are these? I feel like I’m always getting surprised.
But seriously, a rod so strong that people doubt it even functions? That’s insane.
Cheena: Even if the rod does work, it probably bends very slowly. There’s no risk of twisting, either.
Nemoto: If I ever get one, I’ll test it even if the neck is perfectly straight, just for learning purposes.
Cheena: I think they stopped making them, but I’m also curious about the Fender OEM models. Atlansia’s versions were probably stronger, though.
Nemoto: Yeah, Atlansia used to manufacture necks for Fender Japan. Mr. Hayashi said, “Necks made by us don’t warp.” So if you find an exceptionally solid Fender Japan neck, it might be Atlansia-made.
Cheena: That’s totally possible.
Speaking of Atlansia’s unique construction, they also develop their own machines and software.
Nemoto: It’s not unusual to make jigs and small tools, but they even build CNC machines. That’s next-level.
Cheena: These days, home-use CNCs like S-Lab’s “Kuroi Yatsu” (The Black One) and smaller open-source kits like the “CNC 3018” are available, but Atlansia’s work is on an entirely different scale.
Their website has a section for machining tools, but it looks unfinished—it hasn’t been updated since 2007.
Nemoto: Maybe they lost interest, or decided to keep it a trade secret? Their machines use FANUC systems, so they must have fine-tuned them specifically for instrument-making. I’d love to see more details.
Cheena: They also develop control software in-house. For example, they have a fret calculation program that can handle microtonal scales. The Victoria 48 was probably built using that.
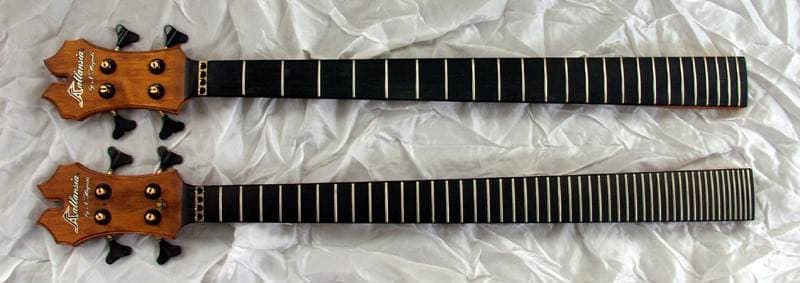
Nemoto: 48 frets... That might appeal to fans of MonoNeon.
I’d also like to check out their router tables. I’m not sure what the optimal size is, though it’s not like I have a CNC, so it wouldn’t matter.
Cheena: For personal use, I think a 120cm × 75cm × 10cm work area would be great. That’s enough to rough-shape a through-neck bass (without an angled joint) or just build regular necks.
That said, Atlansia doesn’t make through-necks. Even when building bodies, the Pegasus model’s horn is divided, so their machines might not be that large.
Nemoto: Umm... I see.
Since Atlansia mainly does bolt-on construction, a smaller setup should be fine. By the way, what CAM software do they use? It’s probably not important, but I’m still curious. Maybe Fusion 360?
Cheena: FANUC likely provides their CAM software. There are some people in the 3D printing community who manually write G-code, but I doubt Atlansia goes that far...
*Fusion 360: A powerful 3D design software by Autodesk that includes CAD, CAM, and simulation features.
*CAM: Software that converts CAD data into machine-processing code (G-code). While G-code itself consists of simple text strings, it allows for convenient specification of complex paths such as arcs in a single line and can apply corrections for the diameter and length of an end mill.
Nemoto: I was totally out of it... Of course, the first option should be the software provided by the manufacturer. It’s the most flexible. But manually inputting commands? No way... Are they a survivor from the era when Linux users controlled behavior through hand-typed commands?
*Nowadays, there are many customized Linux distributions that make things convenient, so manually inputting commands isn't necessary. However, there are still some raw Linux versions where you have to do things manually.
Cheena: I often hear about inserting a pause in the G-code right before changing the Z-axis (height). For example, in 3D printing, pausing before creating the ceiling of a structure allows you to embed nuts or magnets. But if you mess up even once, the whole thing can collapse pretty easily, so it’s tough...
Nemoto: Yeah, exactly. One mistake and it's over... I studied programming a little in the past, and there are some commands that are game over if you mess up—like deleting all data above or below a certain hierarchy. Root privileges are terrifying...
Cheena: That’s exactly why CAM software and virtualized environments have developed so much. Civilization is amazing.
Nemoto: Evolution never stops...
What kind of router bits are they using? Probably straight bits since they’re the safe choice? Or maybe compression bits, though they’re a bit expensive? Well, they’re probably using all kinds, and if they told me they’re using a ton of specialized bits, that’d make sense too. I’m just a little curious which one they use the most.
Cheena: Let’s start with a discussion about router bits...
A straight bit has blades aligned parallel to the bit’s axis. It’s inexpensive but somewhat less effective at chip evacuation in tight spaces. However, it’s useful when trimming the outer edges with a handheld router or trimmer.
Compression or spiral bits have helically shaped blades, and their cutting direction determines their behavior:
- Up-cut spiral: Ejects chips upwards, making cutting easier but leaving rougher edges (similar to a drill bit).
- Down-cut spiral: Leaves cleaner edges but pushes chips down, making cutting more difficult.
- Compression bit: Cuts cleanly on both the edges and the bottom, but it’s expensive and leaves distinctive tool marks at the transition point between the up-cut and down-cut sections.
There are three types.
I’ve never seen photos of parts straight out of a CNC machine, so I can’t say whether they use spiral or straight bits. However, the bits that seem frequently used by Atlantia are ball-end mills, which have a rounded bottom, or round-end mills, which have slightly rounded corners at the bottom. When carving knobs, neck contours, or pickup recesses, using a square-end mill (which has a sharp, square bottom) would be cumbersome and time-consuming.
Of course, for standard neck pockets and pickup cavities, square-end mills are likely used.
Another bit that is almost certainly in use is a slotting bit with a T-shaped profile, where the cutting diameter is larger than the shank. It is a specialized bit used for drilling dowel holes,
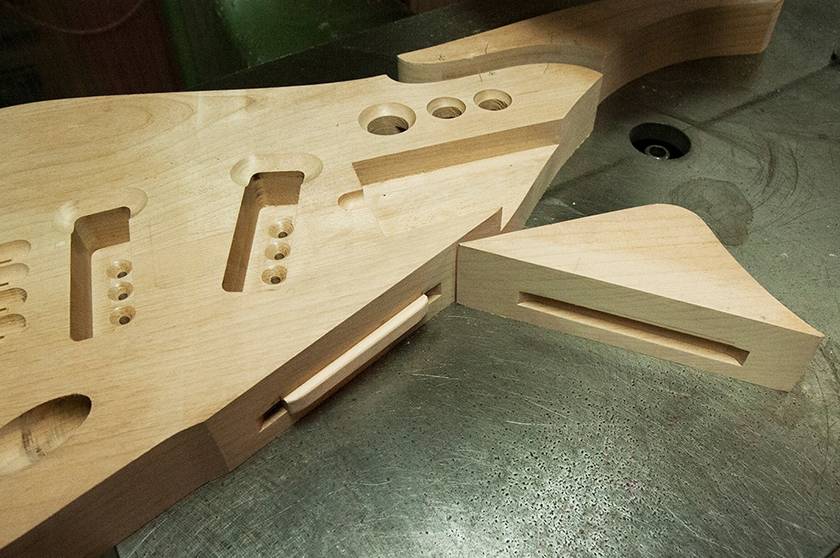
and the joint section of the Pegasus model has dowel holes with rounded ends, a characteristic feature of slotting bits.
Nemoto: Thanks for the detailed explanation. Your ability to deduce from dowel holes is impressive. Bits are surprisingly expensive, and it’s tough for the average person to collect a full set.
Cheena: Technically, you could achieve the same shape by cutting with a square bit while keeping the cut surface facing upward, but in reality, alignment issues make it impractical... unless you’re using a 5-axis NC machine.
Bits are much harder to sharpen compared to planes, chisels, or carving knives. Some can’t even be sharpened at all, which constantly reminds me of just how incredible saw files are.
Also, this part of the Atlansia manufacturing process really caught my attention:
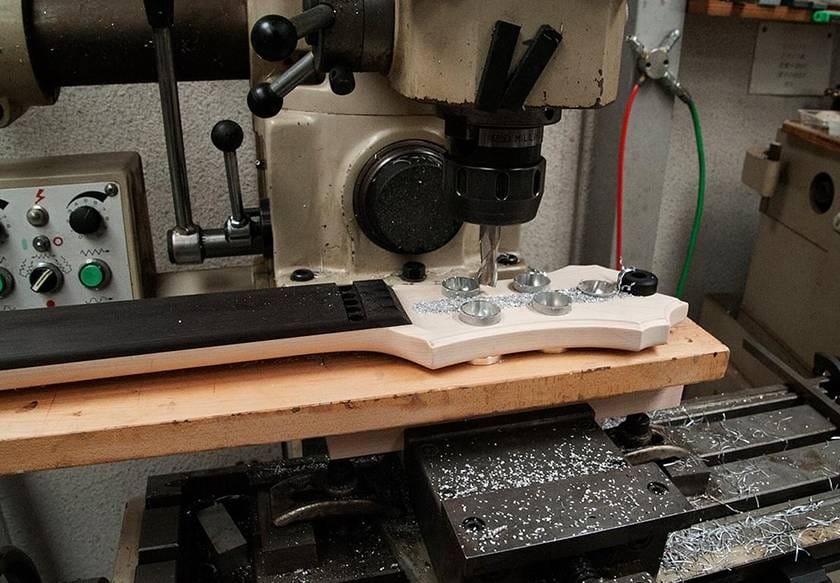
It looks like they're securing the bushing with epoxy and then shaving down the protruding part...
Nemoto: What the...? That’s insane...
Cheena: This is the result.
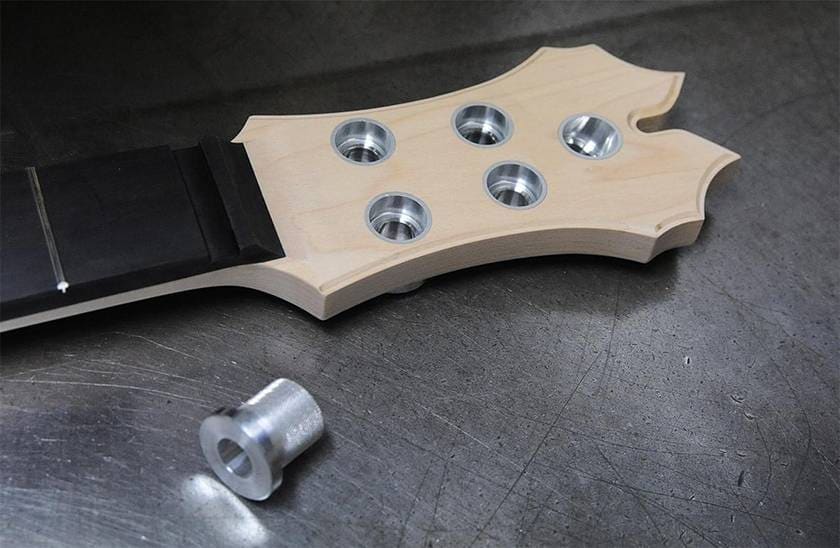

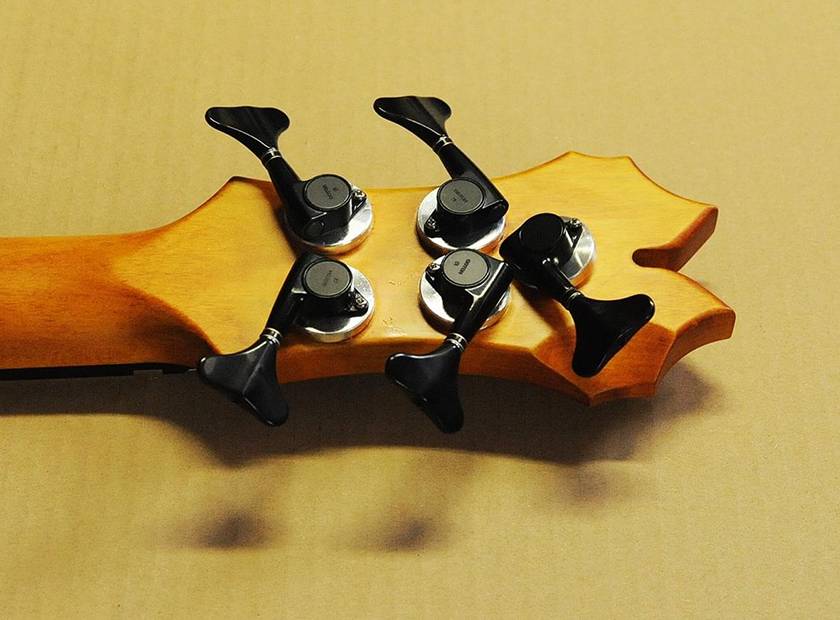
*The 5-string version of the Victoria model features a tuning peg mounted at a 30-degree angle in the center of the headstock, which is otherwise the same as the 4-string version. As a result, the bushing would interfere with the string, so additional processing is done, as shown in the second image above, further shaving it down. The modified section is slightly visible.
Nemoto: I get what they were trying to do, but I never thought they’d actually go through with it.
Cheena: This kind of machining is impossible unless you have absolute confidence in the material’s resistance to cracking and chipping, as well as the precision of the machinery...
Personally, I wouldn’t want to be the one responsible for getting it perfectly flush. But since it’s a flat head, maybe pressing it firmly against the workbench would make it manageable?
Nemoto: They might be using some kind of jig. Even so, it still seems risky... Even if you practice thoroughly on scrap wood, I don’t think the anxiety would completely go away. Maybe I’m just being overly cautious.
Cheena: Judging from the first image, it doesn’t look like they’re using one. They’re probably at least securing the height, but since the cutting conditions for metal and wood are completely opposite (metal requires low-speed rotation, wood requires high-speed), they can’t just plane them down all at once.
Nemoto: No, I meant something that could completely fix the neck at a specific angle to reduce risk... but that’s not a jig. That’s a fixture. My bad. It’d be nice if they could just shave everything down at once, though.
Cheena: If you want to shave everything down at once... a sander would be the way to go. Probably either an orbital or a random-action sander would work.
Nemoto: A sander, huh? Sounds like a pain to finish properly... though I guess that depends on the material.
Cheena: When working with a composite of metal and wood, cooling is going to be a challenge. Might have to resort to liquid nitrogen...
Nemoto: Ah... using a cutting fluid would probably be bad for the wood. It’d stain it.
Cheena: For those well-versed in machining, this probably doesn’t need much explanation, but in metalworking, a liquid coolant is used to reduce friction and provide cooling. This liquid typically contains water and oils, which would be a problem if absorbed by wood. (Not to mention, wood processing doesn’t require it in the first place.) So, we’d have to use something volatile and non-flammable instead.
That said, of course, cooling at the level of liquid nitrogen would cause the metal to contract and freeze the wood, potentially destroying both. So please take that as a dangerous joke...
Nemoto: Liquid nitrogen can explode when it vaporizes (since it expands to 750 times its volume, a poorly chosen container might not withstand the pressure—though as long as it’s not sealed in an unsuitable container, it’s fine). Also, the vaporized nitrogen can cause oxygen depletion (but as long as you’re not in an enclosed space, it’s fine). So seriously, don’t try this.
Cheena: By the way, while it’s technically possible for individuals to purchase liquid nitrogen if cost is no issue, as it evaporates, it can sometimes be replaced by liquid oxygen... which is absolutely something you don’t want anywhere near woodworking.
Anyway, shall we get back on track? Let’s keep liquid nitrogen use limited to cracking lacquer finishes.
Nemoto: OK, what should we talk about next?
2 - Atlansia String Lock Winder
Cheena: I wanted to mention this as an essential topic related to machining and technology, but the information is really scarce. What should I do?
The issue is with the first of two items: the Atlansia Original Design Peg, No.15 String Lock Winder, and No.97 String Winder ‘ShimeShime’.
There’s only a PDF, and the text is barely legible. The patent itself is for a top-lock type peg.
Nemoto: Wasn’t it sealed off? I’ve only seen pictures. It must be really rare for it to be in actual use.
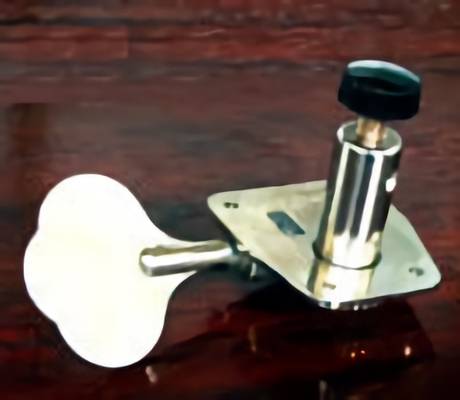
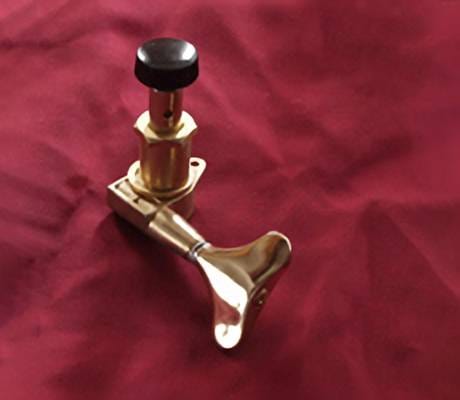
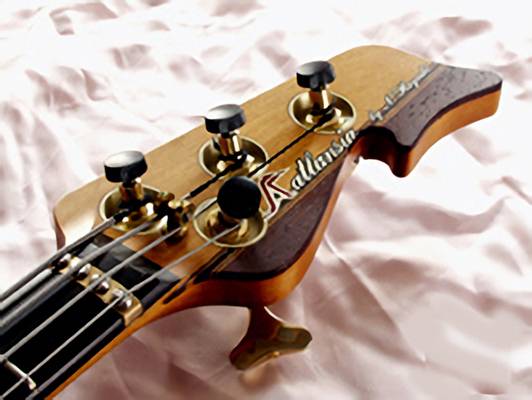
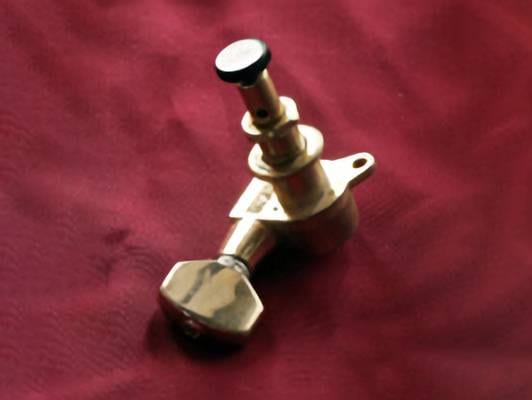
Cheena: Yes, that’s right. The Atlansia patent page says:
“This Winder prevents string loosening, and because the number of wraps on the shaft is minimized, it was patented in 1981. It was published in an official gazette and registered. Later, while dealing with infringement from a Japanese maker, M Co., the U.S. company SP introduced a type that locks from the back. At that point, the dispute was abandoned. Now, it has become a symbolic design, and is still used in some Atlansia models. However, it ended in an incomplete, unfulfilled state without ever seeing widespread success.”
*Source: Atlansia official website
Nemoto: Such a shame. I would have loved to try it.
Cheena: The page itself was last updated around 2001, so if there’s a chance to get one of the top models from that time...
Since the structure of PRS Phase II and Phase III is the same, if this was installed on a bass, it should be quite similar. It’s much simpler than the back-lock or Magnum Lock, so it might be possible to create it with secondary processing or replacing the through-hole shaft. I’ll give it a try next time.
Anyway, we’ll have more wild discussions coming up, but...
Shall we take a break for now?
Nemoto: Sounds good. It’s been quite a long conversation.
Let’s call it a day!
*Image Source: Atlansia Official Website and Facebook
The “sound & person” column is made up of contributions from you.
For details about contributing, click here.