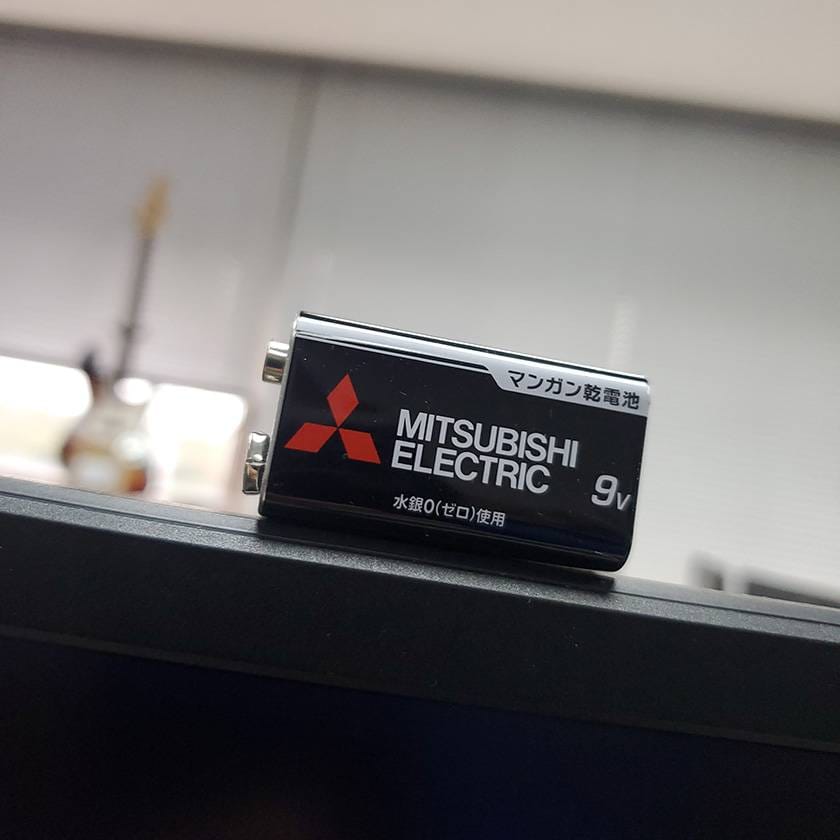
Hello!
I recently learned that placing a pickled plum (umeboshi) on your temples can relieve headaches, and I'm shocked by this.
I always thought it was just a myth, but now I feel like I lost some unspoken battle.
It turns out that benzaldehyde, a compound in the plum’s aroma, has analgesic properties.
While I’m surprised this is actually true, I still can’t quite wrap my head around putting a pickled plum on your temples.
Eating it, or maybe placing it on your forehead, would make more sense, but the temples?
However, considering this information spread across the country even in a time before the internet, I feel a sense of admiration for the pioneer who first relieved their headache by putting a pickled plum on their temples and shared it with the world.
Now, in my previous blog series, I briefly explained how to check if a purchased pickup works, so we’ve finally graduated from “Things to Know About Pickup Replacement” and are moving on to “Things to Know Before Pickup Wiring”.
Let’s start by looking at one of the simpler wirings in electric guitars: the Telecaster.
Or so I’d like to, but before diving into wiring, there are a few things you should know.
Let’s begin with soldering when replacing pickups.
First things first—what is solder?
Take a look at this picture:
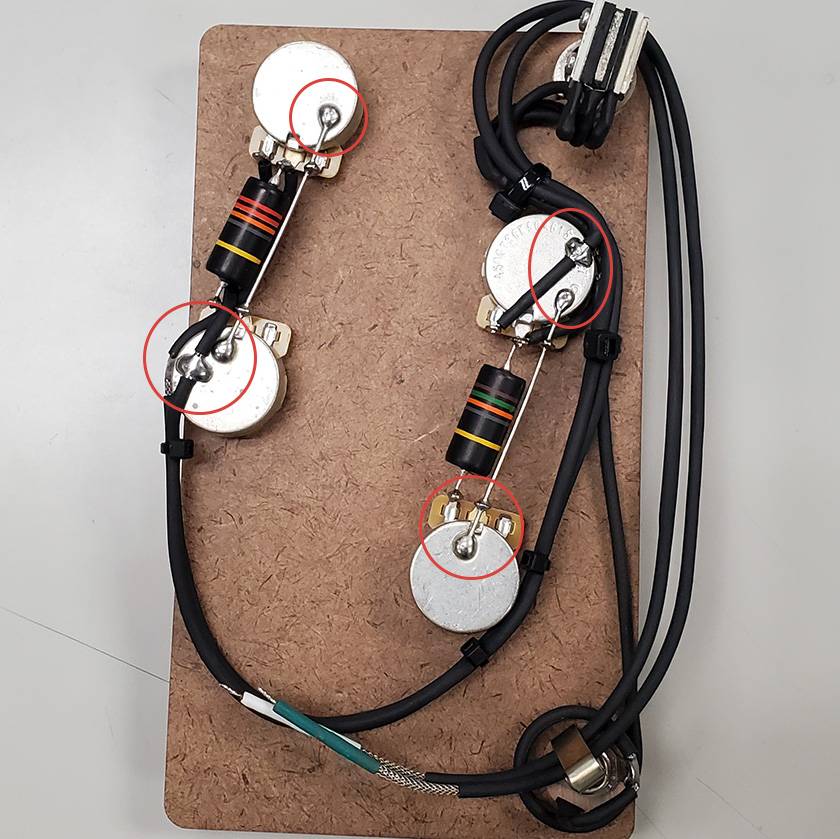
Let’s get closer to it.
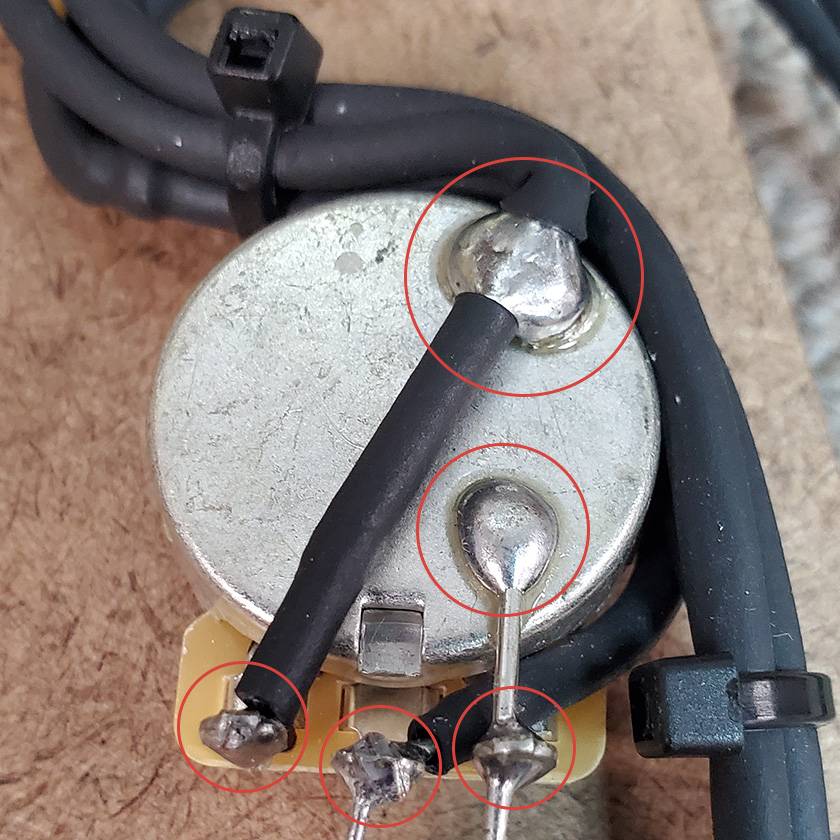
In simple terms, solder is a metal used to connect wiring, similar to welding, you could say.
That’s pretty much its role, but don’t underestimate it.
When you get into specifics like sound quality, it becomes an addictive rabbit hole that can pull you in deep.
By the way, this is an example of soldered wiring:
Emerson Custom / 335 Prewired Kit
We sell pre-wired kits like this one.
Although pickup purchasers or repair shops still need to handle some wiring, these kits reduce the amount of wiring required, making them ideal for those who aren’t too confident in their wiring skills.
Now that the commercial is over, let’s dive into the main topic.
○ Types of Solder
Solder generally falls into two categories: leaded and lead-free.
Leaded solder includes popular products like Kester 44 or 285, which are widely available and easy to find.
It typically consists of about 60% tin and 40% lead, and is known as eutectic solder.
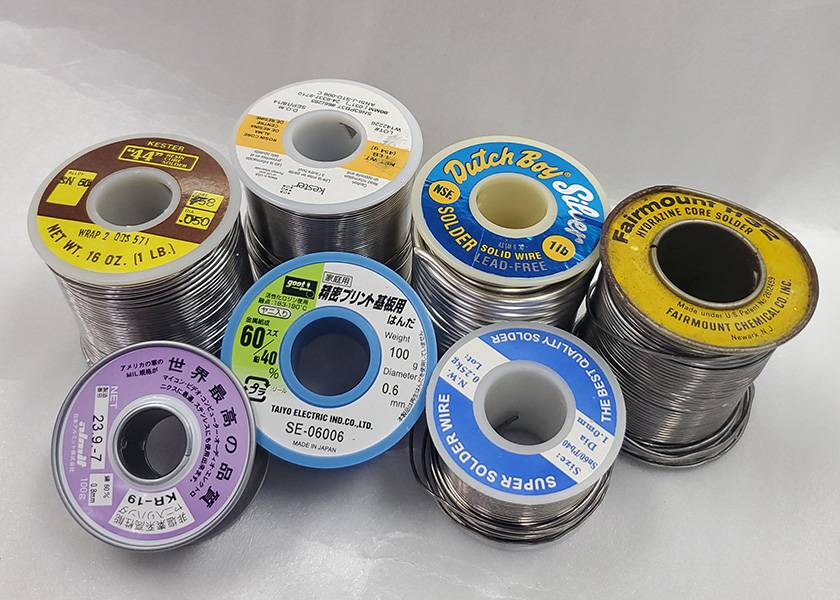
Lead-free solder includes brands like Hakko’s HEXSOL FS600, Nihon Superior’s SN100C, and Oyaide SS-47, which we also carry.
These are often made from tin, silver, and copper or tin, silver, and nickel.
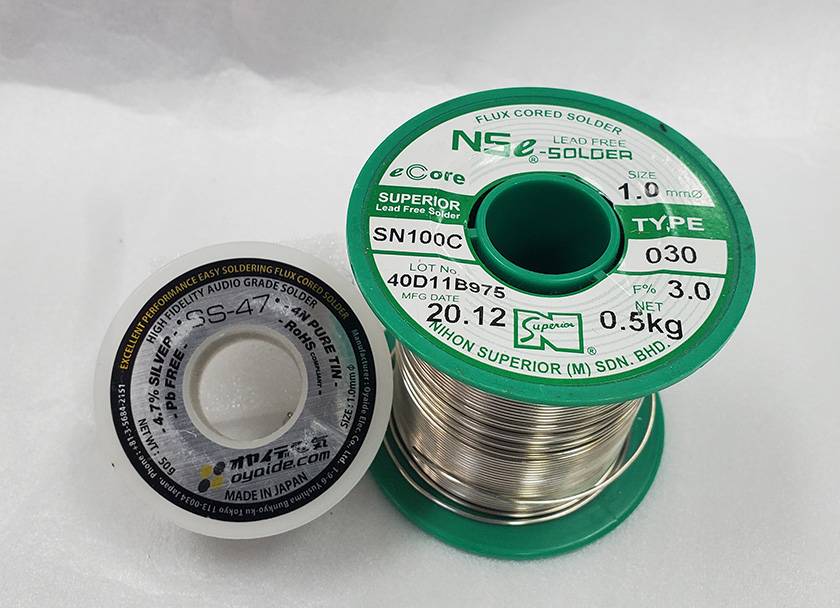
You might wonder:
“Why do both leaded and lead-free options exist?”
That’s because lead is harmful to both human health and the environment.
Inhaling too much smoke during soldering can lead to symptoms like fatigue, headaches, and nausea due to zinc poisoning.
Moreover, when electronics containing lead are disposed of and buried, the lead can seep into groundwater or seawater, posing environmental risks.
There’s also the RoHS directive.
It restricts the use of hazardous substances in electronic equipment in EU countries, and lead is one of the ten regulated substances.
That’s why there are countries where the use of lead is restricted and others where it is not, leading to the existence of both leaded and lead-free solder.
○ Characteristics of Leaded vs. Lead-Free Solder
Since the main components of leaded and lead-free solder are significantly different, their workability and characteristics also vary greatly.
The differences are as follows:
Leaded Solder
- Better wettability
*Wettability: How well solder flows on the metal surface - Lower melting point (around 180°C)
- Higher electrical resistance
- Flux doesn’t scatter much
- Weaker strength
- Heavier compared to lead-free solder
- Has a glossy fillet (the surface after soldering)
Lead-Free Solder
- Poorer wettability
- Higher melting point (around 220°C)
- Flux scatters easily
- Lower electrical resistance
- Stronger strength
- Lighter than leaded solder
- Lacks gloss in the fillet
Another notable difference is the effect on soldering iron tips.
Lead helps protect the tip from oxidizing, so when working with lead-free solder, the tip oxidizes more easily.
Plus, since lead-free solder has a higher melting point, you’ll need to set your iron to a higher temperature.
This shortens the lifespan of the tip by four to five times compared to leaded solder.
○ What is Flux?
Earlier, I mentioned flux in the context of solder differences, so I’m going to quickly explain what flux is.
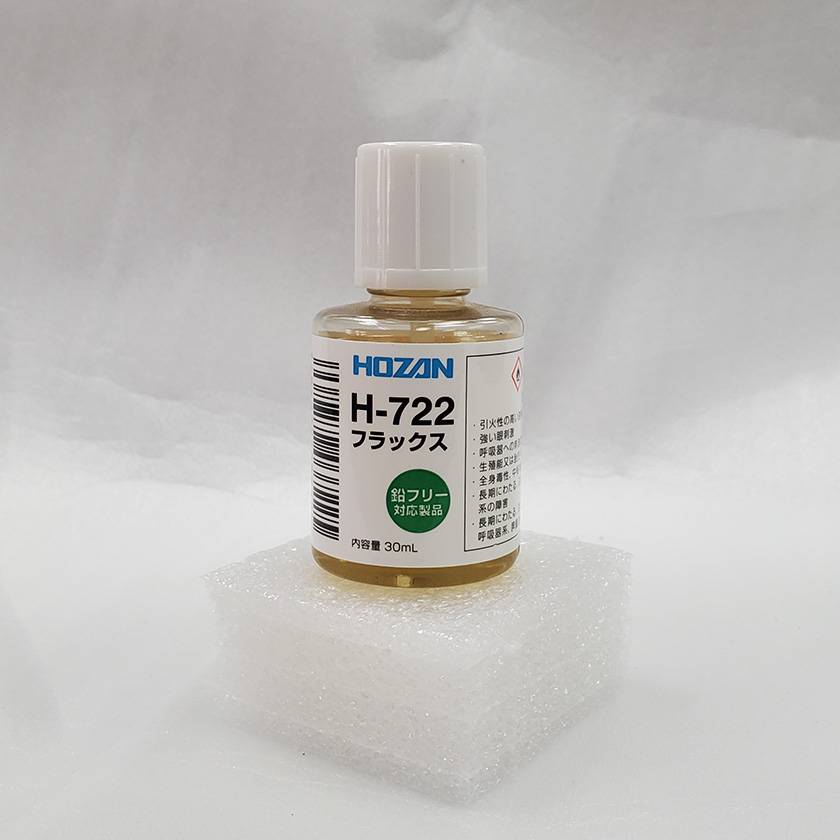
Flux is like an aid that promotes soldering, removing oxidation from the metal surface, improving wettability, and preventing oxidation during the soldering process.
Most flux is made from resin extracted from pine trees, with hydrogen halide salts as activators.
In simple terms, it’s the ‘rosin’ inside the rosin-core solder.
Its role in improving wettability is especially crucial, making wiring with rosin-core solder much easier.
Popular products like Kester 44 are favored partly because their flux formulation makes the solder flow better.
Though many also claim it affects sound quality, that’s a story for another time.
So, what did you think of this introduction to solder?
Both leaded and lead-free types have their pros and cons.
Personally, I prefer lead-free solder due to its environmental benefits, lower electrical resistance, and higher strength. However, lead-free solder is harder to work with.
It melts slower and scatters flux more, making it easy to burn yourself.
Well, there are low-melting-point solders that use bismuth as the main component instead of tin...
So, while I think leaded solder is better for beginners, considering the environmental impact, I’m sorry to say I can’t definitively recommend one over the other.
I can only hope that Japan’s excellent technology will eventually create an easy-to-use, ultimate lead-free solder in the near future.
Until then, see you again on the Sound House staff blog.
Goodbye!