When you first start playing the guitar, you probably won’t worry much about the nut. You might not even notice it except when changing strings.
However, once you’ve been playing for a while, the nut becomes something you start paying attention to.
The nut is the small, usually whiteish part between the fretboard and the headstock. Though it’s not a flashy component, it plays an important role since the strings are supported only by the nut and the bridge saddle. It directly receives the vibrations of the strings, which is crucial for sound.
In general:
① The hardness of the nut determines sound transmission.
② The smoothness of the material affects tuning stability.
Though the nut often goes unnoticed, it plays a significant role in both sound quality and playability.
There are various nut materials, so let’s list a few:
Synthetic Ivory
Since the mid-1960s, many guitar manufacturers started using synthetic ivory. It’s relatively inexpensive and consistent in quality.
At Sound House, Graphtech’s TUSQ is widely available. This product is known for its transparent, clean tone and superior tuning stability, with minimal variation between individual pieces.
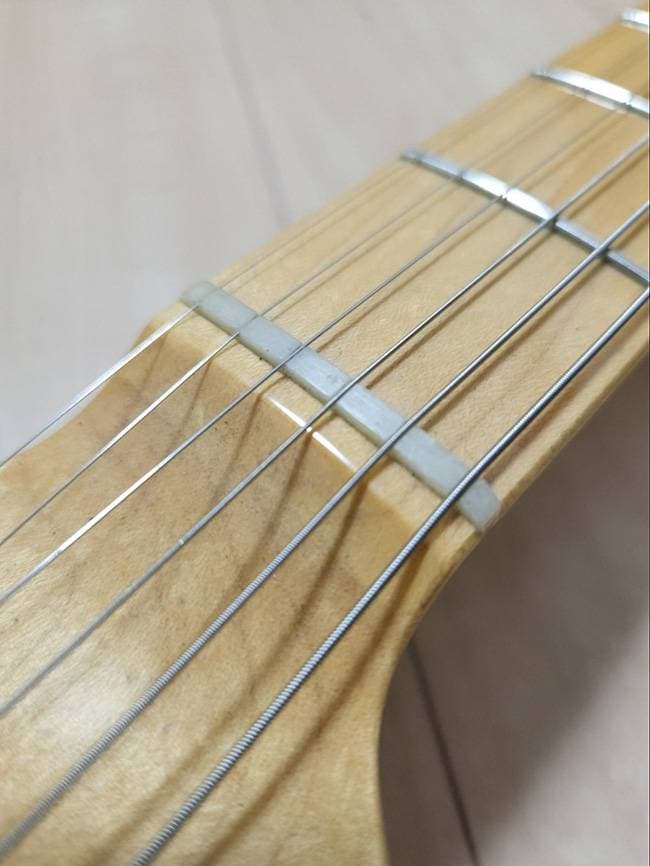
Fender Japan's Nut. An extremely thin and unusual example (on a maple fretboard).
Interestingly, a 1990s Fender Custom Shop order form clearly states ‘Regular (resin)’ for the nut option. While many believe high-end Fender guitars use bone, Custom Shop guitars generally use synthetic resin as well (as shown in the photo).
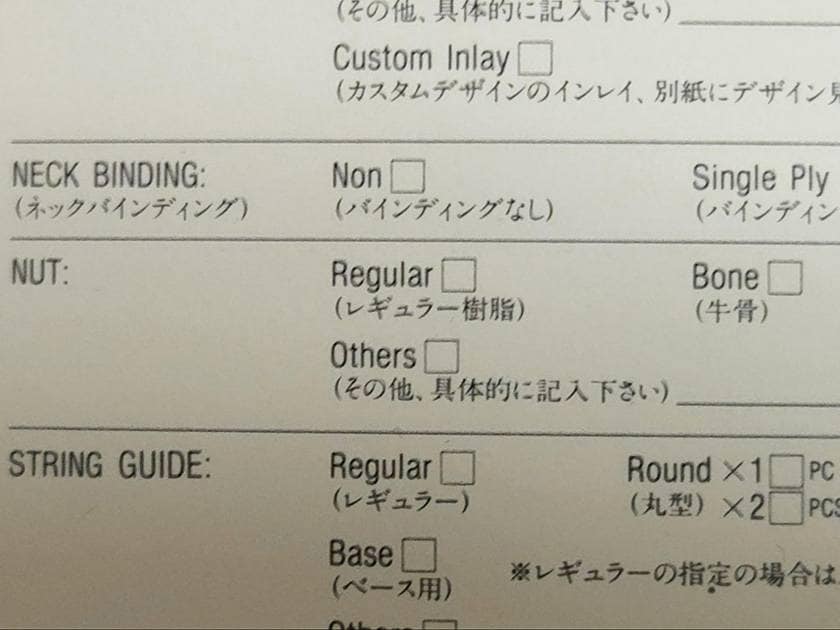
Fender Custom Shop 1990s order sheet. The nut section explicitly states that the regular (resin).
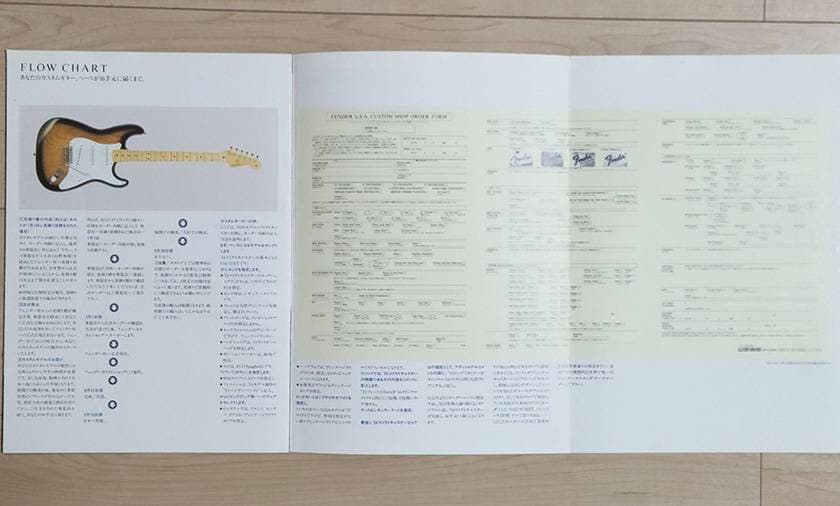
Here’s a sample of a Custom Shop order form.
When I replaced the frets on my 2002 Fender Custom Shop Stratocaster, I also found out it had a synthetic resin nut.
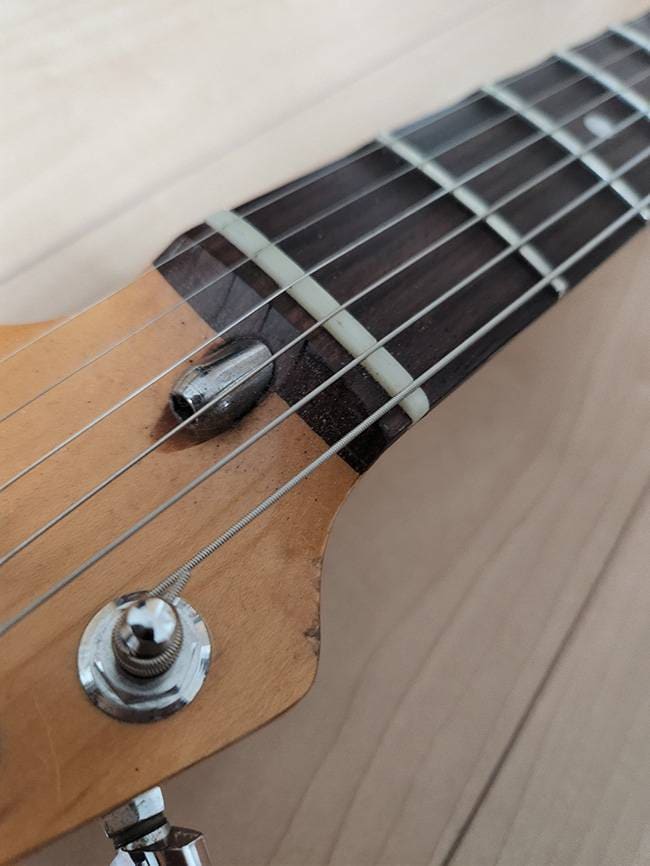
Replacing the nut on a Fender Japan guitar. A bone nut, with a standard shape (on a rosewood fretboard).
Bone
Bone is moderately hard, making it ideal for supporting and transmitting the vibrations of metal strings. It’s also easy to work with and not too expensive. However, bleaching it can sometimes reduce its density.
Still, it’s a popular material used in most guitars, and its sound quality is not compromised as much as people worry.
Oil-Soaked Bone
This type of bone nut has a yellowish tint, as it’s not bleached, preserving the bone’s natural density. The oil helps improve tuning stability. Its vintage look also complements older guitars well. Despite being harder to work with due to the oil content, it’s a popular choice since it’s not much more expensive than bleached bone.
Some repair shops even stock bone nuts soaked in oil.
Example:
SONIC / OB-01 Oiled Bone Nut Fender Style
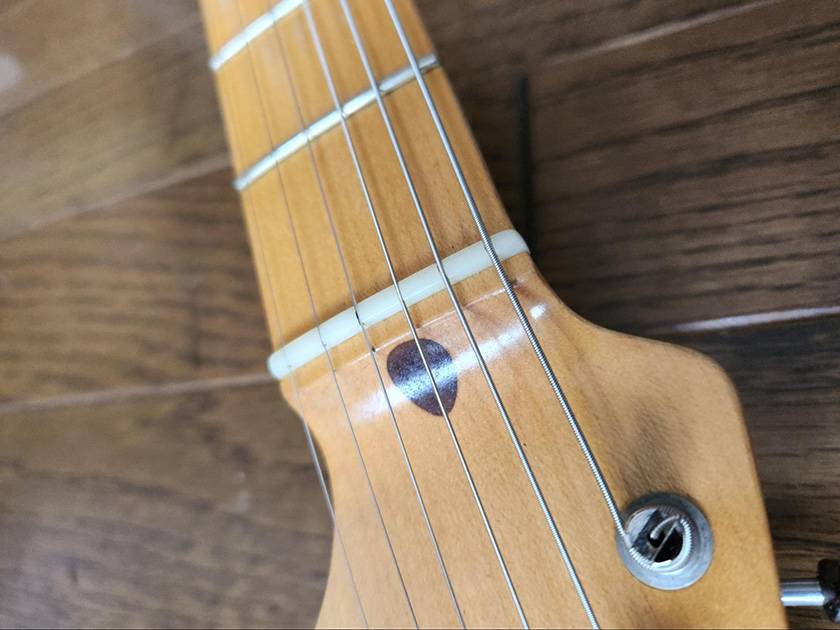
Replacing the nut on a Fender Custom Shop guitar. Nut made of oiled cow bone. Slightly set higher than the original. The labor cost is 8,000 yen (maple fretboard).
Brass
Brass nuts give a somewhat darker, more subdued sound with enhanced sustain. Some guitarists are very particular about using brass nuts.
However, since brass is metal, it’s harder to work with, and repairmen often find it challenging. Without a dust mask, there’s also a health risk, and repair costs are typically high. It’s not an easy material for amateurs to handle.
Brass parts, including nuts, were more commonly used in the early 1980s, but usage has decreased since.
The signature model of Yngwie Malmsteen is well-known for using a brass nut.
I also had a brass nut on a Greco Les Paul flagship model that I owned (from the 1980s).
Carbon Material
The first thing that comes to mind is the Richie Blackmore model, which comes standard with a carbon nut.
Carbon is both hard and smooth, and it’s durable enough to be used in aircraft bodies and car chassis. In other words, it’s lightweight and strong.
Its black appearance can make it stand out more than you might expect.
As with brass, it’s not as widely used as it once was.
Locking Nut
This metal nut is used mainly with Floyd Rose systems. Since it locks the strings with a wrench, tuning remains stable, though returning to the original setup is practically impossible.
Example:
Roller Nut
This nut uses small metal rollers to improve string glide. It’s well-known for being used on Jeff Beck’s signature model. If the rollers wear out, they stop working, but this only happens under extreme circumstances. In case of failure, just replace it. Like the locking nut, it’s not possible to revert to the original setup.
Example:
This is the standard product for roller nuts.
These are the main types of nut materials.
While the nut is a tough and durable part, it’s still a consumable. Since it’s always in contact with the strings, it wears down over time. Arming, in particular, causes more movement on the nut, accelerating wear.
With vintage guitars from the 1950s and 1960s that have been heavily played, it’s common to see the frets and nuts replaced.
Making the six slots in the nut is a delicate work, and any change in string gauge would ideally require adjustment. It’s clear that switching from .09-.42 to .10-.46 strings will cause issues.
For this reason, many guitar repair services offer ‘nut slot cutting’. This is a very delicate task.
The spacing of the nut slots is also a deep and subtle art. It’s not simply about making them evenly spaced for the six strings.
It’s not a matter of measuring with a scale and cutting evenly; a lot of the process relies on the experience and intuition of the craftsman.
Precision is required down to less than a millimeter. The most noticeable effect is on the high E string.
Even a tiny misalignment can cause the string to slip off the frets during vibrato or technical high-fret playing.
This is a common issue with nut replacement.
The playability of the 6th and 1st strings is closely related to nut slotting, so it’s essential to discuss the string spacing thoroughly with your repairman when replacing the nut.
If the nut slotting doesn’t suit your playing style, it can greatly affect playability, leading to frustration.
There’s also a way to improve the smoothness of the nut.
One method is to apply pencil lead powder to the nut slots, or trace them with a mechanical pencil. Both are carbon-based, meaning you can expect the effect of a carbon nut. However, some players may dislike the fact that the nut turns black.
A high-quality nut lubricant called Nut Sauce has been on the market for years and is also available at Sound House. It’s sold overseas too, where it has a great reputation.
It’s said to improve tuning stability. Since it doesn’t damage the guitar, it’s worth trying for guitarists who use the tremolo a lot or are particular about tuning stability.
BigBends / Nut Sauce Lil-Luber
As mentioned earlier, the nut is a consumable part. If it’s excessively worn and the slots get too deep, causing the strings to hit the frets and buzz, it’s time for a replacement.
While it’s not impossible to replace a nut yourself, slotting is a craft, as described above. There are also pre-slotted products available, like those made of synthetic resin.
A search for synthetic resin nuts at Sound House reveals that most products come pre-slotted.
Finally, here’s a tip from my own experience about tremolo adjustments involving the nut.
When using a synchronized tremolo unit, the tuning can go out of whack, but I’ve often found that lightly pressing the area between the nut and tuning pegs on a Stratocaster brings the pitch back to normal.
The “sound & person” column is made up of contributions from you.
For details about contributing, click here.