The synchronized tremolo unit (hereafter referred to as the tremolo unit) was developed over 70 years ago. Originally designed as a subtle effect to add character to music, it became widely adopted as an integral part of guitar playing from the mid-1960s onwards, thanks to pioneers like Jimi Hendrix. Today, it is well-known that numerous evolved versions of tremolo units have been introduced, solidifying their place as an indispensable tool in electric guitar performance.
However, it’s worth keeping in mind, with due respect, that one of its developers, Leo Fender, never envisioned the tremolo unit being used for the intense, highly technical, and bold arming techniques we see today.
When introducing the Stratocaster, one of the most challenging parts to finalize was its tremolo unit. As noted in the U.S. magazine *The Fender Stratocaster*, one of the major obstacles was achieving sufficient sustain, a problem that deeply troubled Leo Fender and his team.
This issue was miraculously resolved by placing a solid block of metal under the bridge plate. However, had this idea come to them any later, the launch of the Stratocaster might have been delayed even further.
Fender's tremolo unit was primarily developed to compete with Bigsby’s vibrato unit. At the time, there were at least five key advantages that set it apart from competing systems:
- Stable Tuning and Wide Pitch Range
It maintained tuning stability while allowing for a broad pitch range, making it easy to set up to personal preferences. - Compact Design
The tremolo unit was small and compact, with a removable arm that could be easily stored. - Adjustability
It offered straightforward adjustments for string height, intonation, and arm tension. - Ease of Repair
Even in the event of wear or failure, replacement parts were widely available, making repairs simple and accessible. - Versatile Sound Changes
Particularly since the 1990s, it has allowed guitarists to explore a wide variety of tonal variations.
The tremolo unit of the 1954 model was constructed using around 50 parts, both large and small. Of these, at least 35 parts can be improved upon with modern advancements.
Let’s explore the parts and products available at Soundhouse that can be purchased and upgraded. This explanation will be divided into two parts. In PART 1, we’ll focus on upgrades starting from the upper portion of the guitar body.
Before making upgrades, there are two important points to keep in mind:
1. Perception of Change Varies by Individual
The sense of improvement is subjective. In this article, I present findings that I am personally confident in, as well as examples gathered from guitar repair technicians and fellow guitarists, aiming to provide as fair and unbiased an assessment as possible. However, it’s possible that some people may not perceive much difference.
2. Upgrade One Part at a Time
Replace parts one by one. If you swap out multiple parts at once, it becomes difficult to identify which change is having what effect. Take a methodical, step-by-step approach.
Now, let’s discuss the changes part by part.
Bridge Plate
Simply put, the bridge plate is a single metal sheet located beneath the saddles. On budget Strat-type guitars, it's likely manufactured at a cost of just a few hundred yen. Replacing it requires fully disassembling the tremolo system, and reassembling it with proper saddle adjustments can be challenging to do on your own. I opted to have a professional guitar repair technician handle the installation.
This is an expensive upgrade, and not cost-effective by typical standards, so it’s not something most would choose to replace. However, considering that the bridge plate directly interacts with string vibrations, I decided to invest over 10,000 yen—roughly the cost of a budget guitar—to upgrade it.
The result? A noticeable improvement! The sound became warmer and more resonant, with a distinct richness that was impossible to miss. Although I don’t personally use the tremolo arm much, the plate's edge finishing was excellent, enabling smoother and more stable arm usage with less tuning instability.
Upgrading the bridge plate right out of the gate turned out to be one of the most impactful modifications I’ve made. For me, this was the most impressive improvement, delivering tangible results that left me thoroughly satisfied.
CALLAHAM / Top Plate for Vintage S Model Bridge
Saddles
Among the components of the tremolo unit, saddles are one of the parts where replacing them makes the most noticeable difference in sound. They are available in a variety of materials, including steel, titanium, brass, and zinc die-cast. The original Strat saddles were made of steel, which is a safe and reliable choice due to its excellent response and attack.
Titanium is a more expensive material due to its difficulty in processing but is widely recognized in the industry. Brands like KTS are pioneers in replacement parts, offering titanium saddles that deliver a clear and transparent tone, making them stand out.
Brass saddles gained popularity around the 1980s, primarily aimed at increasing sustain. In addition, they are known for producing a warm and full-bodied sound.
Zinc die-cast saddles, which have been mounted on Stratocasters since the 1970s, have sparked mixed opinions. Personally, I feel they faithfully reproduce the sound of the music scenes of that era. Despite differing views, I find their tonal qualities entirely acceptable, producing a bright and powerful sound that works well in many contexts.
Fender's current stock saddles deliver a standard and classic tone.
FENDER / AMERICAN VINTAGE STRATOCASTER BRIDGE SADDLES (6)
If you want to go a step further with Fender, consider those with the "PAT. PEND" engraving.
FENDER / Pure Vintage Stratocaster "Pat. Pend." Saddle Kit
KTS saddles are known for their clean, transparent tone and enhanced sustain.
KTS / PR-11 For Synchronized Tremolo US pitch 11.2mm
RAW VINTAGE saddles offer a natural tone with excellent separation.
Callaham saddles have a slightly sharp tonal character.
CALLAHAM / Vintage S Model "CG" Saddle Set
Gotoh saddles are excellent value for money
Saddle Height Screws (Grub Screws)
Though less than a centimeter in size, these tiny components play a significant role in tone, as they directly transmit string vibrations from the saddle to the body. For more detailed insights, refer to my column, "Excellent value! Change the set screws to adjust the sound quality.", where I explore this topic in depth. I encourage you to read it and try this upgrade yourself.
To put it simply:
- Nickel material offers a natural and balanced tone.
- Stainless steel provides a powerful, clear, and modern sound.
Montreux / Stainless Steel (Round Type)
Montreux / Stainless Steel (Core Type)
Tremolo Arm
The tremolo arm is a stylish part that moves the tremolo unit and also affects the guitar's appearance. There are various differences, such as material, length, bend angle (design), and thickness. Materials are broadly divided into steel and stainless steel. The latter is more durable and resistant to breaking but tends to be more expensive.
David Gilmour is famous for using a short arm. Jeff Beck has long used an arm with an angled tip that fits snugly in the palm of his right hand.
In the 1970s, Ritchie Blackmore used an extremely thick arm for intense arming and, in the mid-1980s, briefly adopted a curved arm known as the "moon-shaped style arm." Personally, I believe this style is more suited for quick vibrato techniques using the entire hand and arm rather than extreme pitch changes.
Callaham arms are designed with threads only at the tip, making them resistant to bending inside the tremolo block and less prone to wobbling. They come in both long and short versions and are highly recommended (compatible only with Callaham blocks).
A classic model with an angled design.
MONTREUX / SC tremolo arm inch chrome w/white tip [8420]
Short arm.
MONTREUX / Montreux DG Stainless Arm Inch ver.2[9116]
RB-type moon arm.
MONTREUX / Montreux RB Moon Stainless Arm Inch [9689]
Available in three different lengths.
CALLAHAM / Virtual Pop-in Tremolo Arm STD-Fender, Parchment White
A thick arm with a diameter of 6mm.
MONTREUX / Tremolo Arm 6mm Chrome [9708]
Some modifications may be necessary to fit these into a standard tremolo block.
The Soundhouse products introduced here are just a few examples of the parts I personally used for modifications. The website offers a wide variety of other products, so I encourage you to explore and consider them. Find the components that will help you craft your original sound.
In PART 2, we’ll focus on modifying the rear body parts.
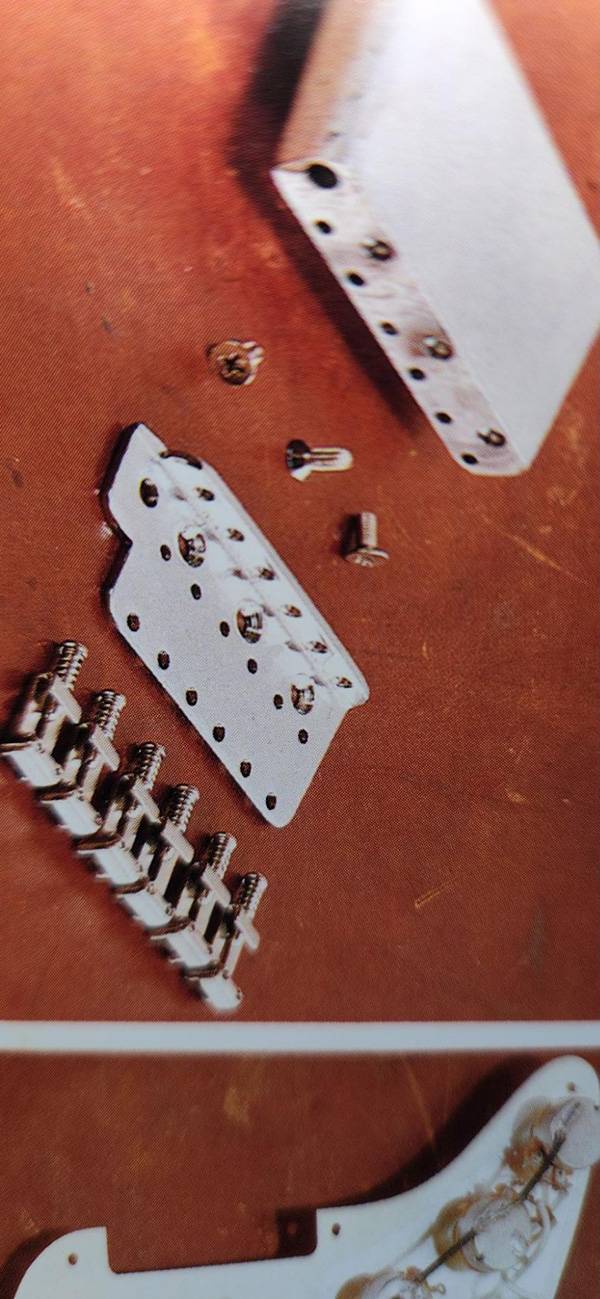
From a 1980s Fernandes catalog.
The “sound & person” column is made up of contributions from you.
For details about contributing, click here.